Introduction to Sizing Agent AKD and Wet Strength Resins
The effective sizing and strengthening of paper are crucial factors in the paper manufacturing industry. In order to achieve desired properties such as water resistance, printability, and dimensional stability, the utilization of sizing agents and wet strength resins is imperative. This article provides an in-depth exploration of sizing agent AKD (Alkyl Ketene Dimer) and wet strength resins in the context of the paper industry. It aims to shed light on their roles, applications, challenges, and best practices, enabling paper manufacturers to optimize their processes and enhance the quality and performance of their paper products. Understanding the significance and proper utilization of AKD and wet strength resins is essential for achieving efficient and sustainable paper production.
Sizing Agent AKD and Wet Strength Resins
Overview of Sizing Agents in Paper Industries
When it comes to paper manufacturing, sizing agents play a crucial role in enhancing the performance and durability of the final product. These agents are responsible for reducing the paper’s absorbency, allowing it to resist water and liquid penetration. This not only improves the print quality but also prevents ink spread and maintains the paper’s structural integrity.
Introduction to AKD (Alkyl Ketene Dimer)
One popular sizing agent used in the paper industry is AKD, also known as Alkyl Ketene Dimer. AKD is a synthetic chemical compound that is widely recognized for its excellent sizing properties. It is commonly used due to its biodegradability, low toxicity, and compatibility with different paper grades. AKD works by forming a hydrophobic layer on the paper surface, which repels liquids and enhances the paper’s resistance to water.
Introduction to Wet Strength Resins
In addition to sizing agents, wet strength resins are another essential component in the paper manufacturing process. As the name suggests, wet strength resins are responsible for imparting strength and stability to the paper when it is wet. These resins help prevent the paper from disintegrating or losing its structural integrity when exposed to water or high humidity conditions. This is particularly important for applications such as packaging and tissue paper, where wet strength is crucial.
Understanding the Role of Sizing Agent AKD in Paper Industries
Importance of Sizing in Paper Manufacturing
Sizing is a critical step in paper manufacturing as it directly affects the paper’s printability, ink holdout, and resistance to moisture. Without proper sizing, ink can bleed and spread on the paper surface, resulting in fuzzy text and poor image quality. Sizing agents like AKD help control the paper’s surface properties, allowing for crisp and vibrant prints while preventing unwanted blotting or smudging.
Mechanism and Benefits of AKD Sizing
The mechanism behind AKD sizing involves the reaction between AKD molecules and the cellulose fibers in the paper. This chemical reaction forms a water-repellent layer on the paper surface, effectively reducing its absorbency. The benefits of AKD sizing include improved print quality, increased ink holdout, enhanced water resistance, and improved dimensional stability of the paper.
Effects of AKD Sizing on Paper Properties
AKD sizing not only affects the paper’s surface characteristics but also impacts its physical and mechanical properties. Sizing with AKD can improve the paper’s tensile strength, tear resistance, and folding endurance. Additionally, AKD sizing can enhance the paper’s resistance to aging and yellowing, prolonging its lifespan. With AKD, you can have paper that not only looks great but also performs exceptionally well.
The Importance of Wet Strength Resins in Paper Manufacturing
Understanding Wet Strength and its Significance
Wet strength refers to a paper’s ability to maintain its strength and integrity even when exposed to water or high levels of humidity. This property is crucial for various applications like tissue paper, tea bags, and packaging, where the paper needs to retain its strength even when wet. Wet strength resins are added to the paper pulp to improve its resistance to water, preventing the paper from disintegrating or losing its shape.
Types of Wet Strength Resins
There are different types of wet strength resins used in the paper industry, including melamine-formaldehyde (MF), urea-formaldehyde (UF), and polyamidoamine-epichlorohydrin (PAE) resins. Each type has its own unique characteristics, such as varying levels of wet strength and compatibility with different paper grades. The choice of resin depends on the specific requirements of the paper application.
Applications and Benefits of Wet Strength Resins in Paper Industries
Wet strength resins find extensive applications in industries where water resistance is crucial. These resins are widely used in the manufacturing of tissue paper, paper towels, food packaging, and labels. The benefits of using wet strength resins include improved durability, resistance to tearing when wet, increased shelf life, and enhanced product performance, even in high-humidity environments.
Factors to Consider in Sizing Agent AKD Application
Paper Grade and Specific Requirements
The choice and application of AKD sizing depend on the paper grade and specific requirements. Different paper grades have varying absorbency levels and surface characteristics, which may necessitate adjustments in AKD dosage and concentration. Understanding the paper’s intended purpose and its unique demands is crucial in achieving optimal sizing results.
Optimal Dosage and Concentration
Determining the optimal dosage and concentration of AKD sizing agents is essential for achieving the desired results. Too little AKD may result in inadequate sizing, while excessive amounts can lead to undesirable effects like increased stiffness or reduced brightness. Finding the right balance is key to ensuring the paper meets the required specifications.
Effect of pH and Temperature on AKD Sizing
The pH and temperature conditions during the AKD sizing process can significantly impact its effectiveness. AKD sizing works best at slightly acidic or neutral pH levels, and higher temperatures generally lead to better sizing efficiency. However, extreme pH levels or temperatures can affect the reaction kinetics and compromise the performance of AKD sizing. Careful control of these factors is necessary to achieve optimal results.
Guidelines for Proper Application of Wet Strength Resins
Determining Wet Strength Requirements
When it comes to using wet strength resins in paper industries, it’s important to first determine the wet strength requirements. Consider the specific application of the paper and the level of moisture resistance needed. This will help in identifying the appropriate wet strength resin to use.
Selecting the Right Type and Concentration of Wet Strength Resin
Choosing the right type and concentration of wet strength resin is crucial for achieving the desired results. Different resins offer varying levels of wet strength, so it’s important to consider the specific requirements of your application. Additionally, the concentration of the resin will also impact the final outcome. Pay attention to the manufacturer’s guidelines and conduct thorough testing to ensure optimal performance.
Methods of Application and Implications
The method of application of wet strength resins can significantly impact the overall effectiveness. Factors such as the application technique, equipment used, and timing of application all play a role. It’s important to follow recommended application methods and adjust according to specific production variables. Improper application can result in insufficient wet strength or even adverse effects on paper quality.
Challenges and Solutions in Sizing Agent AKD and Wet Strength Resin Usage
Common Challenges Faced in AKD Sizing and Wet Strength Resin Application
Using sizing agent AKD and wet strength resins in paper industries can come with its fair share of challenges. Some common issues include uneven distribution of the chemicals, variations in paper quality, or inadequate wet strength. Understanding these challenges is the first step towards finding solutions and improving the overall process.
Troubleshooting and Problem-solving Techniques
When faced with challenges in AKD sizing and wet strength resin application, employing troubleshooting techniques is essential. This may involve adjusting the application parameters, optimizing process conditions, or exploring alternative resin options. It’s important to identify the root cause of the problem and implement effective solutions to ensure consistent and high-quality results.
Best Practices for Sizing Agent AKD and Wet Strength Resin Selection and Optimization
Quality Control and Testing Methods
To ensure the selection and optimization of sizing agent AKD and wet strength resins, incorporating quality control measures is crucial. Regular testing of paper properties, wet strength, and other relevant parameters can help in identifying any deviations and taking prompt corrective actions. Maintaining consistent quality control practices throughout the production process is key to achieving desired outcomes.
Optimizing Process Parameters for Maximum Efficiency
Optimizing process parameters is a vital part of maximizing efficiency in sizing agent AKD and wet strength resin usage. This includes controlling variables such as temperature, pH levels, mixing times, and curing conditions. Adjusting these parameters to find the optimal balance can improve the performance of the chemicals and minimize waste.
Ensuring Compliance with Environmental Regulations
In addition to efficiency and quality, it’s important to pay attention to environmental regulations when using sizing agent AKD and wet strength resins. Ensure that the chosen products comply with local regulations and adopt environmentally friendly practices wherever possible. This includes proper disposal of chemicals, adherence to safety guidelines, and minimizing the impact on the environment.
Maximizing Efficiency and Quality in Paper Industry Sizing Processes
In conclusion, proper application of sizing agent AKD and wet strength resins is crucial for achieving desired wet strength properties in paper industries. Understanding wet strength requirements, selecting the right resin type and concentration, employing appropriate application methods, and troubleshooting challenges are key to success. By following best practices, optimizing process parameters, and ensuring compliance with regulations, paper manufacturers can maximize efficiency and quality in sizing processes, resulting in superior end-products. So, go forth and conquer the world of paper sizing, one wet strength at a time!
Conclusion
sizing agent AKD and wet strength resins play integral roles in the paper manufacturing industry. By utilizing AKD sizing, paper manufacturers can enhance water resistance and printability, while wet strength resins provide the necessary strength and durability. Understanding the factors to consider in their application, troubleshooting challenges, and implementing best practices can lead to optimized processes and improved paper quality. By continuously striving for efficiency and adhering to environmental regulations, the paper industry can achieve sustainable and high-quality paper production. Through the proper selection and utilization of sizing agent AKD and wet strength resins, paper manufacturers can ensure their products meet the demanding requirements of various applications in today’s market.
FAQ
What is the role of sizing agent AKD in paper industries?
AKD (Alkyl Ketene Dimer) sizing agent is used in paper industries to impart water resistance, dimensional stability, and printability to paper products. It forms a hydrophobic barrier on the paper surface, preventing excessive absorption of water and improving ink holdout.
How do wet strength resins benefit paper manufacturing?
Wet strength resins are essential additives that enhance the strength and durability of paper, particularly when exposed to moisture. They improve the paper’s resistance to tearing, bursting, and disintegration when wet, allowing for applications like packaging, labels, and wet-conditions environments.
What factors should be considered when applying sizing agent AKD?
Key factors to consider in AKD sizing application include the paper grade and its specific requirements, optimal dosage and concentration of AKD, and the influence of pH and temperature. Understanding these factors ensures effective and consistent sizing results.
How can paper manufacturers optimize the selection and usage of wet strength resins
To optimize the selection and usage of wet strength resins, paper manufacturers should determine their specific wet strength requirements, select the appropriate type and concentration of resin, and carefully consider the methods of application. Additionally, conducting quality control tests and complying with environmental regulations are vital steps in maximizing the efficiency and quality of the paper sizing process.
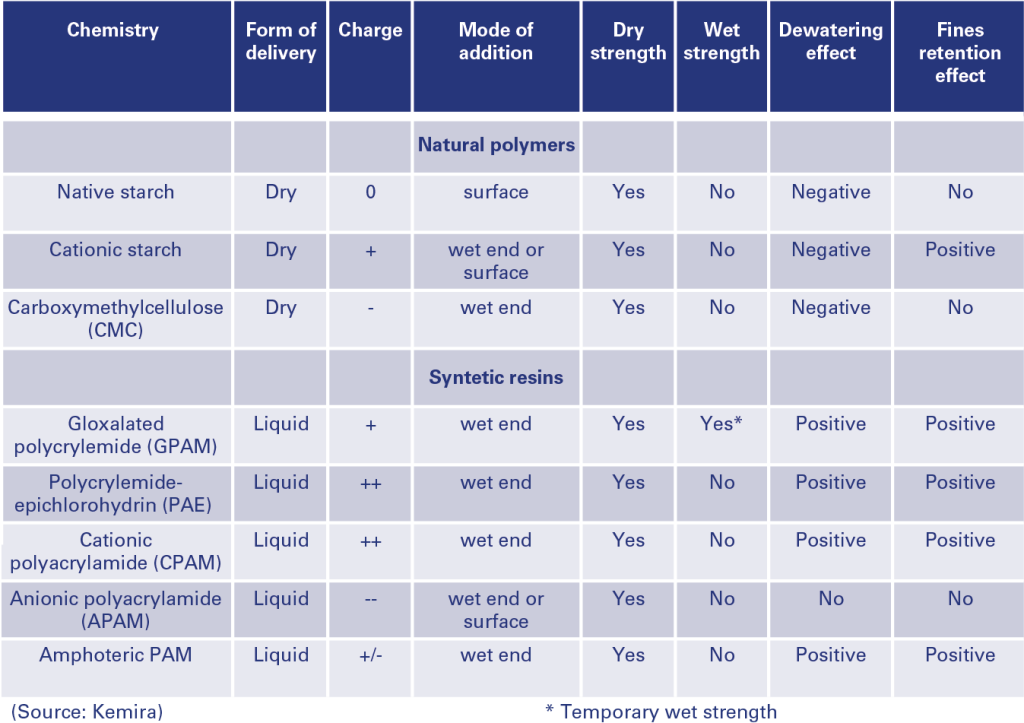
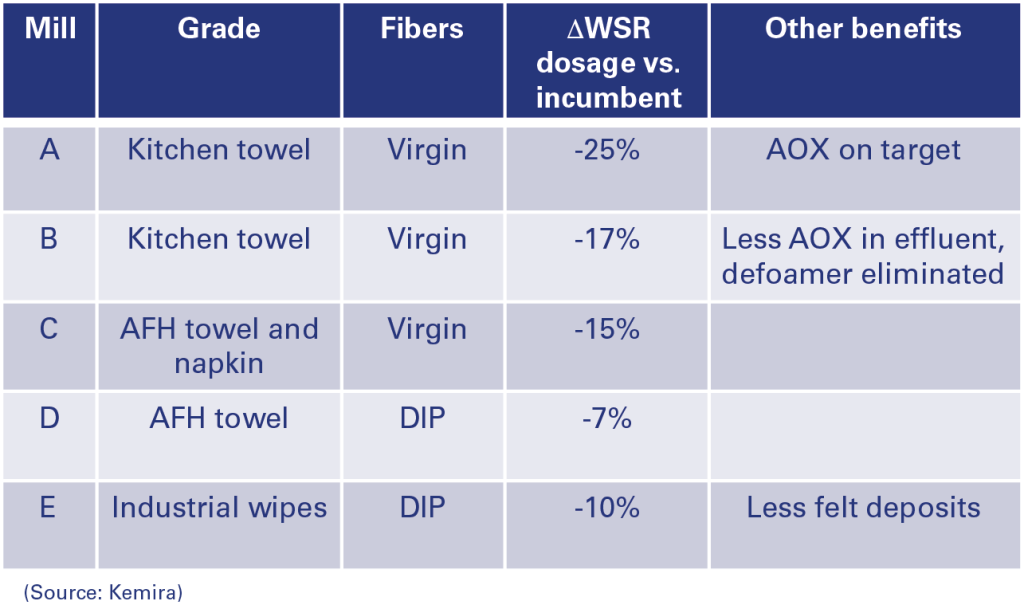
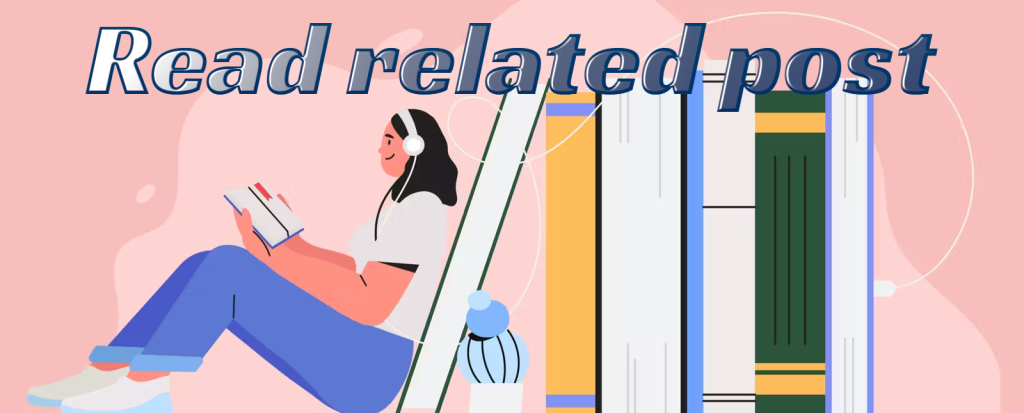





