Internal and external sizing are two distinct techniques used in paper manufacturing to improve the physical properties of paper and enhance its performance in various applications. The key difference between internal and external sizing lies in the location where the sizing agents are added onto the paper.
1.Internal sizing
involves the incorporation of sizing agents into the paper furnish during the papermaking process. Sizing agents are added to the pulp before it is formed into paper, and they become an integral part of the paper fibers. These agents work by forming a thin film or coating around the individual fibers, making them resistant to liquid penetration. Internal sizing protects the paper from absorbing aqueous liquids, such as ink or water, thereby improving its printability and resistance to smudging.
2.External sizing
on the other hand, involves the application of sizing agents onto the surface of the paper after it has been formed. This process is usually done using size presses or sprays, where the sizing agents are either applied uniformly or selectively to specific areas of the paper surface. External sizing serves to enhance the paper’s properties, such as water repellency, ink holdout, and print quality. It forms a protective layer on the paper surface, preventing the ink or other liquids from penetrating and spreading, thereby improving the paper’s print quality and durability.
3.While
the primary goal of both internal and external sizing is to improve the paper’s resistance to liquid penetration. there are some differences in terms of effectiveness and application.
Internal sizing is typically more effective in preventing ink feathering and bleeding. as the sizing agents are integrated into the fibers, providing a more uniform protection throughout the paper. It is especially important for porous paper, such as newsprint or absorbent papers, where ink bleeding can be a significant issue.
4.External sizing
on the other hand, is more commonly used for papers that require higher print quality and precise control over the application of sizing agents. This technique is often used in coated papers, such as glossy magazines or high-quality printing papers. By applying the sizing agents on the surface, external sizing can create a more controlled and uniform coating, resulting in superior printability and ink holdout.
It is worth noting that both internal and external sizing are not mutually exclusive, and they can be used together to achieve optimal paper performance. In many paper manufacturing processes, both techniques are employed to take advantage of their respective benefits. By combining internal and external sizing, manufacturers can create papers that offer excellent properties, such as high print quality, ink holdout, and resistance to liquid penetration.
Conclusion
In conclusion, internal sizing involves the addition of sizing agents to the paper furnish during the papermaking process. While external sizing includes the application of sizing agents onto the surface of the formed paper.
Internal sizing integrates the sizing agents into the fibers, offering more uniform protection against liquid penetration. While external sizing provides a controlled and precise coating on the paper surface. Both techniques have their unique advantages and are often used together to enhance the properties of the paper for specific applications.
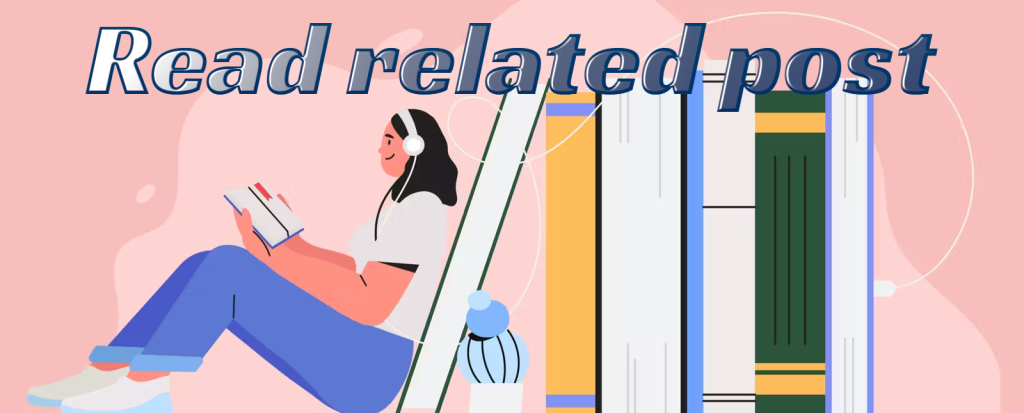