Aluminum is one of the most abundant metals on Earth and has a wide range of applications in various industries. Its production process involves several crucial steps, starting from the extraction of aluminum from bauxite ore to the final refining. This essay will focus on the aluminum production process, with a particular emphasis on the use of aluminum fluoride.
First step
The first step in the production process is the extraction of aluminum from bauxite ore. Bauxite is primarily composed of aluminum oxide minerals, such as gibbsite, boehmite, and diaspore. The ore is crushed and refined into a white powder called alumina through the Bayer process. During this process, bauxite is mixed with sodium hydroxide, which dissolves the alumina while impurities remain as a red mud waste.
Second Step
After the alumina is extracted, it undergoes the Hall-Heroult process to convert it into aluminum metal. This process involves the electrolysis of alumina dissolved in molten cryolite, a mixture of sodium, aluminum, and fluorine compounds. To optimize the overall efficiency of the electrolysis, aluminum fluoride is added. Aluminum fluoride acts as a flux, reducing the melting point of cryolite and improving the conductivity of the electrolyte, thus reducing energy consumption.
The addition of aluminum fluoride also helps to maintain the stability of the molten electrolyte. The high temperatures and corrosive nature of the electrolyte can lead to the formation of metal impurities, such as iron and silicon, which can hinder the production process. Aluminum fluoride forms stable complexes with these impurities, preventing their deposition on the cathode and improving the purity of the obtained aluminum metal.
Another important role
Moreover, aluminum fluoride plays a crucial role in controlling the composition of the electrolyte. During the electrolysis, the concentration of aluminum fluoride decreases due to its participation in the reaction. To maintain the desired composition, fresh aluminum fluoride is continuously added. By controlling the concentration of aluminum fluoride, the overall effectiveness of the Hall-Heroult process can be enhanced.
In addition to its role in the Hall-Heroult process, aluminum fluoride finds applications in other areas of aluminum production as well. In the production of aluminum alloys, aluminum fluoride is often used as a catalyst to promote the purification and homogenization of the molten metal. It can also enhance the mechanical properties of the alloy by reducing the presence of harmful elements, such as hydrogen and oxygen.
Aluminum fluoride is a vital component in the production process of aluminum, as it contributes to the efficiency, stability, and purity of the obtained metal. It acts as a flux, reduces the melting point of the electrolyte, enhances the conductivity, and prevents the formation of metal impurities. Additionally, it plays a crucial role in maintaining the desired composition of the electrolyte and has applications in the production of aluminum alloys. Overall, the use of aluminum fluoride in the aluminum production process is essential for the sustainable and efficient production of this versatile metal.
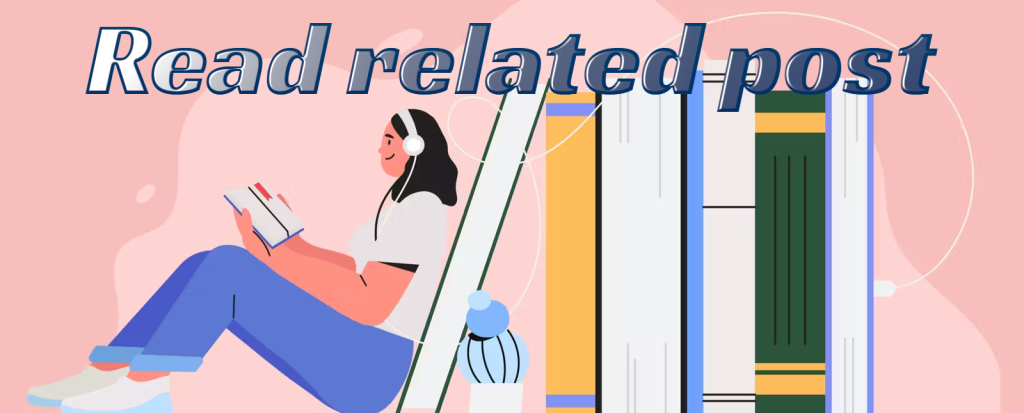