Introduction:
Membrane electrolyzers have emerged as a promising technology in the production of caustic soda, playing a crucial role in various industries worldwide. This comparative study aims to analyze different types of membrane electrolyzers used in caustic soda production, highlighting their principles, benefits, and performance. By examining the advancements in membrane electrolyzers and comparing them to traditional diaphragm electrolyzers, this article aims to provide a comprehensive understanding of the membrane electrolysis process and its significance in the production of caustic soda. Additionally, economic and environmental considerations in choosing membrane electrolyzers will be discussed, along with insights into future prospects and research directions in this rapidly evolving field. With the increasing demand for caustic soda, it is essential to explore efficient and sustainable technologies like membrane electrolyzers to meet industrial requirements and minimize environmental impact.
1. Membrane Electrolyzers
1.1. What are membrane electrolyzers?
Membrane electrolyzers are a type of electrochemical device used in the production of caustic soda. They utilize a selective membrane to separate the anode and cathode compartments, allowing for the controlled ion transport during the electrolysis process. This technology has gained popularity due to its efficiency and ability to produce high-quality caustic soda.
1.2. Historical development of membrane electrolyzers
The development of membrane electrolyzers can be attributed to the continuous efforts of scientists and engineers in improving the caustic soda production process. While diaphragm electrolyzers were initially used, the limitations of this technology led to the exploration of more advanced alternatives. Membrane electrolyzers were first introduced in the late 20th century, marked by the development of ion exchange membranes capable of withstanding harsh electrolytic conditions. Since then, continuous research and advancements have led to the widespread adoption of membrane electrolyzers in the industry.
Related Post: EVOLUTION OF BRINE ELECTROLYSIS: A JOURNEY THROUGH THE HISTORY OF CAUSTIC SODA PRODUCTION
2. Overview of Caustic Soda Production
2.1. Importance of caustic soda in various industries
Caustic soda, also known as sodium hydroxide, plays a critical role in a wide range of industries. It is a key component in the manufacturing of products such as soaps, detergents, paper, textiles, and various chemicals. Additionally, caustic soda is extensively used in water treatment, petroleum refining, and wastewater treatment processes. Its versatility and importance make it a vital commodity in global industrial operations.
2.2. Traditional methods of caustic soda production
Historically, the production of caustic soda involved the use of diaphragm electrolyzers. These electrolyzers utilize a porous diaphragm to separate the anode and cathode compartments, allowing for the controlled migration of ions. However, the use of diaphragms posed challenges such as inefficiencies, limited operating current densities, and the release of environmentally harmful chlorine gas. Over time, the industry shifted towards membrane electrolyzers as a more advanced and sustainable solution.
3. Traditional Diaphragm Electrolyzers: Function and Challenges
3.1 Working principle of diaphragm electrolyzers
In diaphragm electrolyzers, the anode and cathode compartments are separated by a porous diaphragm. The diaphragm selectively allows the migration of sodium ions while blocking the passage of chloride ions and other impurities. During the electrolysis process, a direct electric current is applied, causing the formation of chlorine gas at the anode and hydrogen gas at the cathode. Simultaneously, sodium ions migrate through the diaphragm, reacting with hydroxide ions to produce caustic soda.
3.2. Limitations and challenges of diaphragm electrolyzers
Although diaphragm electrolyzers were widely used in the past, they presented several limitations. One major challenge was the limited operating current densities, resulting in low production rates. The release of chlorine gas as a byproduct also posed environmental concerns. In addition, the presence of impurities in the brine solution could cause fouling and damage to the diaphragm, reducing its lifespan. These challenges prompted the development of membrane electrolyzers as a more efficient and sustainable alternative.
4. Advancements in Membrane Electrolyzers: Principles and Benefits
4.1. Introduction to membrane electrolysis technology
Membrane electrolysis technology utilizes ion exchange membranes to separate the anode and cathode compartments. These membranes selectively allow the migration of specific ions, enabling the controlled production of caustic soda. The use of membranes overcomes the challenges faced by diaphragm electrolyzers and offers improved efficiency, higher current densities, and reduced environmental impact.
4.2. Advantages of membrane electrolyzers over diaphragm electrolyzers
Compared to diaphragm electrolyzers, membrane electrolyzers offer several significant advantages. They allow for higher operating current densities, resulting in increased production rates and improved energy efficiency. The elimination of chlorine gas as a byproduct reduces environmental pollution and eliminates the need for chlorine gas handling and disposal. Additionally, membrane electrolyzers have longer lifespans, as they are less susceptible to fouling and damage from impurities in the brine solution.
4.3 Role of membranes in improving efficiency and product quality
The selective membranes used in membrane electrolyzers play a crucial role in enhancing efficiency and product quality. They facilitate the migration of sodium ions while blocking impurities and unwanted ions. This selective transport helps maintain a high concentration of sodium hydroxide in the cathode compartment, resulting in the production of high-purity caustic soda. Additionally, the membranes contribute to minimizing energy losses and improving overall system performance, making membrane electrolyzers a preferred choice in modern caustic soda production.
5. Comparison of Different Types of Membrane Electrolyzers
5.1. Proton exchange membranes (PEMs)
Proton exchange membranes (PEMs) are like the cheerleaders of the electrolyzer world. Just like a supportive cheerleader, PEMs are efficient and enthusiastic in facilitating the electrolysis process. They have high proton conductivity, which allows them to separate the hydrogen ions from other elements during electrolysis. This means they can produce caustic soda with great precision and accuracy. PEMs are like the overachievers of the membrane electrolyzer family, always striving for top-notch performance.
5.2. Anion exchange membranes (AEMs)
Anion exchange membranes (AEMs) are the reliable and level-headed siblings of the membrane electrolyzer family. They work with a calm and composed demeanor, effortlessly separating the anions and cations during the electrolysis process. AEMs possess good chemical stability and can withstand harsh conditions, making them suitable for long-term use. They may not be as flashy as PEMs, but they are dependable and get the job done consistently.
5.3. Biَpolar membranes (BPMs)
They are the multi-talented siblings that can do it all. Like a Swiss Army knife, BPMs have a dual personality, acting as both anion and cation exchange membranes. This versatility allows them to separate both anions and cations simultaneously during electrolysis, making them efficient and resourceful. However, their complexity comes with a trade-off as they require careful optimization and maintenance.
5.4. Performance and characteristics of each membrane type
In terms of performance, PEMs often lead the pack with their high efficiency and excellent selectivity. AEMs follow closely behind, providing consistent performance and durability. BPMs, while versatile, require more fine-tuning to achieve optimal performance. Each membrane type has its unique characteristics, and the choice ultimately depends on the specific requirements of the caustic soda production process.
6. Performance Evaluation of Membrane Electrolyzers in Caustic Soda Production
6.1. Efficiency and productivity analysis of membrane electrolyzers
Efficiency and productivity are crucial factors in caustic soda production. Evaluating the performance of membrane electrolyzers involves analyzing their energy consumption, current efficiency, and production rates. Higher energy efficiency and current efficiency indicate more economical and sustainable operation, while increased production rates contribute to meeting demand. These evaluations help determine the optimal membrane electrolyzer for maximizing caustic soda production.
6.2. Electrolysis process optimization for caustic soda production
Optimizing the electrolysis process is like fine-tuning a recipe for caustic soda production. Factors such as current density, temperature, and electrolyte concentration influence the efficiency and yield of the electrolysis process. Understanding the interplay between these variables allows for process optimization, resulting in improved caustic soda production. It’s like finding the perfect mix of ingredients to create the best batch of caustic soda.
Related Post: UNVEILING THE CAUSTIC SODA INDUSTRY: ELECTROLYSIS PLANTS VS. FLAKING UNITS
7. Economic and Environmental Considerations in Choosing Membrane Electrolyzers
7.1. Cost analysis of membrane electrolyzers
Let’s talk money! Choosing the right membrane electrolyzer involves considering the initial investment, operational costs, and maintenance expenses. While PEMs may be efficient performers, they tend to be more expensive upfront. AEMs, on the other hand, offer a balance of performance and affordability. Conducting a cost analysis helps determine the most financially viable option for caustic soda production.
7.2. Environmental impact and sustainability of membrane electrolysis
Being environmentally conscious is crucial in today’s world. Fortunately, membrane electrolysis offers a greener alternative to traditional methods. By using renewable energy sources and minimizing the use of harmful chemicals, membrane electrolyzers reduce carbon emissions and environmental impact. They also promote sustainability by improving resource efficiency and minimizing waste. Choosing a membrane electrolyzer with lower environmental impact contributes to a cleaner and more sustainable caustic soda production process.
8. Future Prospects and Research Directions in Membrane Electrolyzer Technology
8.1. Current research trends and developments
The membrane electrolyzer world is constantly evolving, with researchers exploring new frontiers. Current trends focus on improving membrane durability, enhancing proton and anion conductivity, and increasing overall efficiency. Explorations into advanced materials and novel manufacturing methods pave the way for exciting advancements in membrane electrolyzer technology. Stay tuned for the latest breakthroughs!
8.2. Potential advancements and innovations in membrane electrolyzer technology
The future of membrane electrolyzer technology holds immense promise. Advancements in materials science, such as developing new ion exchange polymers, may revolutionize membrane performance. Additionally, integrating artificial intelligence and smart control systems can optimize electrolysis processes for maximum efficiency. The potential for advancements and innovations in membrane electrolyzer technology is limitless, and the future looks brighter than ever. Let’s raise a glass of caustic soda to that!
In conclusion, this comparative study has shed light on the various types of membrane electrolyzers used in caustic soda production. The advancements in membrane electrolysis technology offer significant advantages over traditional diaphragm electrolyzers, including improved efficiency, product quality, and sustainability. The performance evaluation of membrane electrolyzers showcased their potential for enhancing the caustic soda production process. Moreover, economic considerations and environmental implications emphasized the importance of selecting the most suitable membrane electrolyzer. As research and development in this field continue to flourish, the future holds promising prospects for further advancements and innovations in membrane electrolyzer technology. By embracing these advancements, industries can meet the growing demand for caustic soda while minimizing their environmental footprint.
Related Post: The Effects of Temperature on the Reaction Rate between Caustic Soda and Water
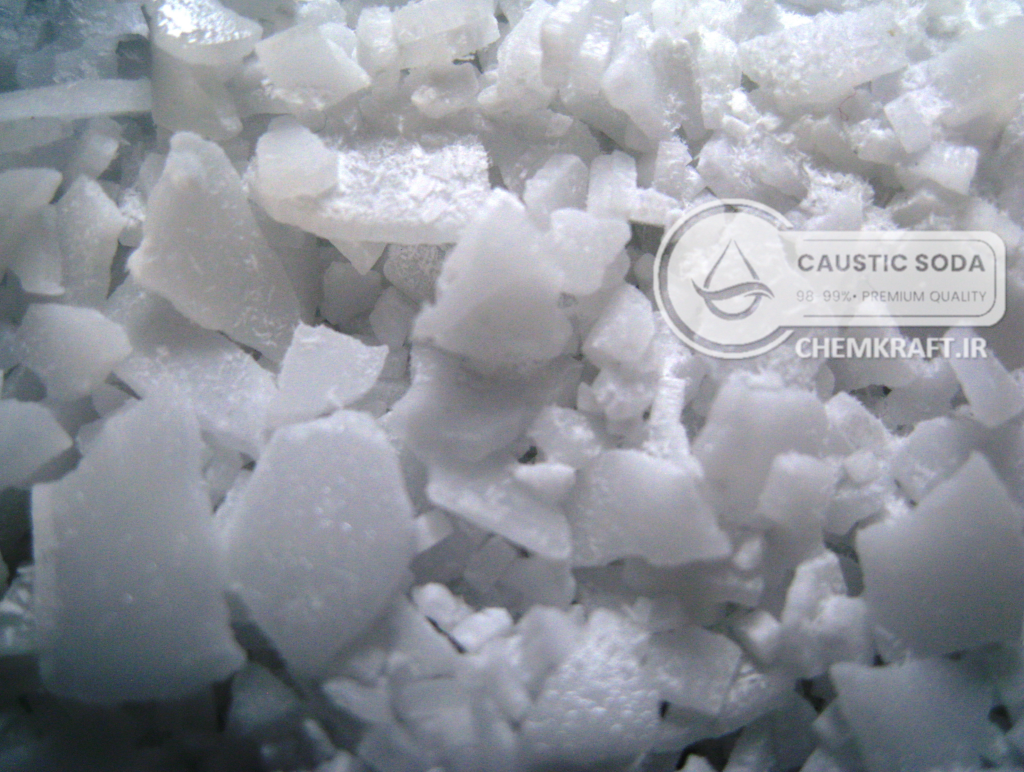