About AKD sizing
AKD is an active sizing agent, which can react with the hydroxyl group of cellulose to form an irreversible covalent bond, and the sizing effect is stable.
The AKD sizing mechanism consists of three main steps:
1) AKD emulsion particles are attached to the fiber surface.
2) AKD is heated in the drying section and spreads on the fiber surface.
3) AKD reacts with hydroxyl groups of cellulose to form covalent bonds.
Using AKD emulsion for neutral sizing can lead to sludge formation in the system. To control this, manufacturers add fungicides during production and, if necessary, shut down the system for cleaning. Factors affecting AKD neutral sizing mainly include the following aspects:
PH value
Since the AKD reaction occurs under neutral conditions, manufacturers must carefully control the pH of the slurry and the system when adding AKD. The optimum pH range is between 7 and 8. When the pH value is less than 6, AKD is completely ineffective. Therefore, when the system is changed from acidic to neutral, in addition to thoroughly scrubbing the system, the amount of AKD should be increased or even doubled.
Retention
Generally, AKD sizing needs to add retention aids. Due to the addition of PAE wet strength agent, in addition to increasing the wet strength, it also has a synergistic effect on AKD retention.
PAE (polyamide epichlorohydrin) not only has a retention effect in the wet end, but also participates in the sizing reaction of AKD when the paper sheet is dry.
Research shows that heating paper turns the PAE resin into a nucleophile, promoting the opening of the AKD lactone ring and attaching it to the PAE resin macromolecular chain.
PAE resin has a high bridging ability. It can be irreversibly fixed on the surface of the fiber, so that AKD is irreversibly bonded to the surface of the fiber through the intermediate reaction with PAE.
Add point
AKD undergoes a hydrolysis reaction in water to form a product without sizing, and this hydrolysis reaction accelerates as the temperature rises. At the same time, severe shearing action should be avoided.
The shearing action will damage the AKD emulsion. So, in order to reduce In the loss of AKD in papermaking the addition point should be as close as possible to the forming section.
Temperature
When the temperature does not meet the reaction requirements, the sizing reaction cannot occur.
Controlling the drying temperature and conditions is an important factor to ensure the sizing effect.
The starting point of the sizing reaction should not be lower than 95°C.
The paper mill should set the appropriate temperature and time according to different drying methods.
Production findings show that, while maintaining the desired sizing degree, using less AKD yields better results.
When the amount of AKD exceeds the optimum value the decrease in cobb (absorbency) value will slow down, and at the same time, the friction coefficient of the paper will decrease, and the paper will Slippage, difficult production.
The paper sizing degree of AKD sizing has hysteresis.
Manufacturers typically store the material for 7-10 days after production to gradually achieve the desired sizing effect.
Therefore, in order to timely measure the sizing degree of the unmachined paper sample.
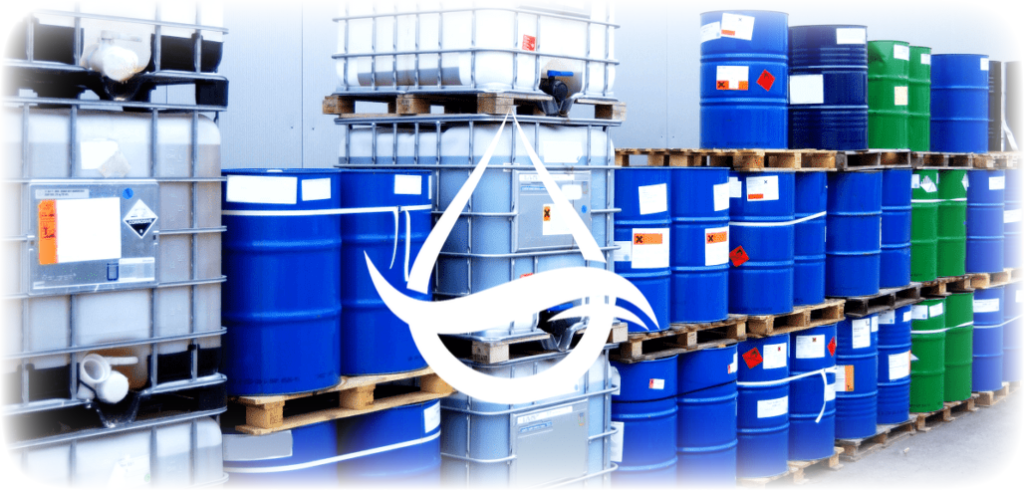
it is necessary to accelerate the sizing ripening degree by drying in an oven at 105°C for 10 minutes.
The result measured at this time is the final sizing degree.
In summer, paper sizing by AKD does not have the problem of sizing difficulty, it is easy to dry and does not need emulsified rosin.
Economic calculations show that the cost per ton of paper is lower than that of acid papermaking, while paper strength increases by approximately 10%.
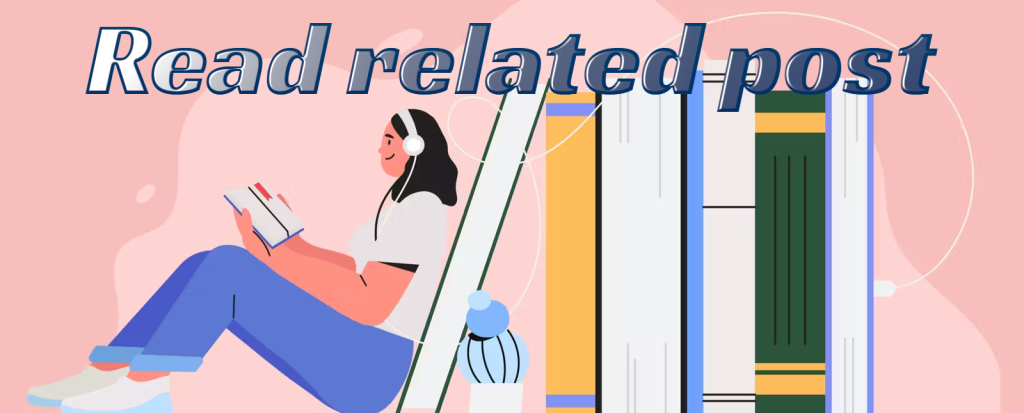





