About Wet Strength Resins
Definitions
PAE is capable of working in alkaline and neutral papermaking processes. This material establishes covalent bonds with fibers and by creating a network in the cellulose substrate, when the paper gets wet, it provides its strength and resistance.
Also, these resins improve the overall strength of the paper by strengthening the leaf-leaf bonds.
Cationic oxalated polyacrylamide (GPAM) is a strength-enhancing resin that is often used as a dry strength-enhancing resin.
The polyacrylamide chain includes small amounts of cationic monomer such as dimethyl ammonium chloride (DADMAC) which causes the self-maintenance of the polymer on the fibers.
This situation is shown in the figure below (adapted from TAPPI documents).
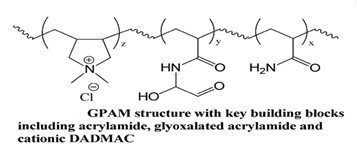
What is GPAM
GPAM is a polymer with the ability to form a re-covalent bond with cellulose during the drying of the cellulose network. This process results in paper that has improved both wet and dry resistance. In an aqueous medium, the reaction with cellulose can be reversed. When dry paper is exposed to a wet environment, the bond between cellulose and the polymer slowly breaks down. This is why GPAM is known as a ‘resin for increasing temporary wet resistance.’ It does not cause blockages in sewage systems, and the paper structure breaks apart as the napkin enters the sewers. Likewise, this feature in paper factories causes the conversion of Brook Pulper to take place with less energy consumption.
Also, the molecular structure of GPAM is such that it can control the decay rate of wet resistance. Controlling the decay rate of resistance is important according to the type of paper, so that in tissue paper (and especially toilet paper), the decay rate must be fast. But in cardboard and cardboard, the decay rate should be slower.
Applications
The use of temporary wet resistance increasing resin in cardboard and cardboard can improve RCT, CMT, SCT resistance, burst resistance, tensile strength and surface resistance. The mechanism of action in this case includes strengthening the connections between fibers by bonding. covalent bonds and hydrogen bonds.
This material also improves the water absorption of the sheet in the press section, in addition to this, the drainage (in the wire section) also increases.
In PAE, the linkages are not easily hydrolyzed. PAE creates a waterproof layer around the leaf-leaf points, which prevents the destruction of hydrogen bonds by water. The use of this resin in tissue (especially paper towels) should be controlled in such a way that it does not reduce the smoothness of the surface.
In papers used for producing cartons and boxes in humid environments, such as those shipped by sea or in regions with high relative humidity (like the north and south of our country), manufacturers typically use 5-7 kg of this resin per ton of paper. 5-7 kg/ton) can significantly improve the efficiency and durability of cartons in these climates and produce high-quality cartons.
In tissue papers, the highest consumption of this resin should be in napkins, conventional papers such as tea bags (such as paper tea bags), sanitary napkins, baby diapers, hospital and operating room towels and sheets. In toilet paper, it is better to use the temporary wet resistance resin mentioned above.
Brief about wet resistance increasing resins
Wet resistance increasing resins are divided into two categories:
1) wet strength agent
2) temporary wet strength agent
The materials of the first group are based on the molecular structure of PAE and the materials of the second group are based on the molecular structure of GPAM.
Advantages
The use of Wet strength resins has the following advantages:
1-Improved wet resistance
2-Improvement of retention and drainage
3-Creating better control conditions on cropping operation
4-Improve dry resistance
5-Reducing the cost of chemicals
6-Improving the efficiency and having a positive effect on the speed of the paper machine





