Advantages and disadvantages of sizing
In the paper industry, sizing refers to the process of treating paper with various chemical substances to improve its physical properties. Sizing can be accomplished using internal sizing or external sizing methods.
Both techniques offer distinct advantages and disadvantages, which are crucial for paper manufacturers to consider for optimal paper production. This essay will discuss the advantages and disadvantages of internal and external sizing in the paper industry.
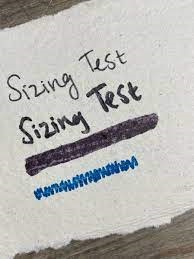
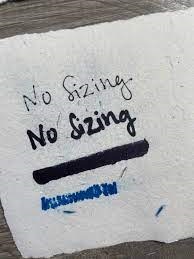
:Advantages of internal sizing
Internal sizing involves adding sizing agents directly into the paper pulp during the papermaking process.
One of the main advantages of internal sizing is that it provides uniform and predictable sizing throughout the entire paper sheet.
This leads to better print quality, as it prevents ink from feathering or bleeding on the paper’s surface. Additionally, internal sizing improves resistance to liquid penetration, making it ideal for applications such as packaging materials or books where moisture resistance is essential.
Another advantage of internal sizing is that it can enhance the strength and durability of paper. By reinforcing the paper fibers, internal sizing can increase resistance to tearing and folding, resulting in a more robust final product.
Moreover, internal sizing promotes paper’s dimensional stability, reducing the tendency for the paper to curl or warp when exposed to changes in humidity or temperature.
:Disadvantages of internal sizing
However, internal sizing has its drawbacks as well. One disadvantage is that certain sizing agents used in the internal sizing process can negatively impact the environment.
Some commonly used internal sizing agents, such as rosin and synthetic sizes, can release volatile organic compounds (VOCs) during production, contributing to air pollution.
Additionally, the wastewater generated from internal sizing often requires intensive treatment to remove the sizing chemicals before it can be safely discharged, resulting in increased operational costs for paper mills.
: Advantages of external sizing
On the other hand, external sizing involves applying sizing agents to the surface of the paper sheet after it has been formed.
External sizing offers several advantages, including greater flexibility and control over sizing properties.
Paper manufacturers can easily modify the amount and composition of the sizing agents according to specific requirements.
External sizing also allows for easier experimentation and optimization of sizing formulas, as changes can be made without affecting the entire paper production process.
Furthermore, external sizing is more environmentally friendly compared to internal sizing.
Many of the sizing agents used in external sizing, such as starch or polyvinyl alcohol, are biodegradable and exhibit lower toxicity levels.
This makes the waste generated during external sizing easier to treat and less harmful to the environment.
:Disadvantages of external sizing
However, external sizing has certain disadvantages as well.
One drawback is that it may be less effective in providing consistent and uniform sizing throughout the paper sheet.
External sizing tends to affect the surface more than the interior of the paper, which can lead to variations in sizing performance. This inconsistency may result in uneven ink absorption or insufficient liquid resistance.
Another disadvantage of external sizing is that it may increase the paper’s surface roughness.
Sizing agents coated on the paper’s surface can cause a slight roughness, impacting the paper’s smoothness and printability.
In applications where high print quality is crucial, such as magazines or books with detailed images, the roughness caused by external sizing may be undesirable.
:Conclusion
both internal and external sizing methods have advantages and disadvantages in the paper industry.
Internal sizing offers better uniformity, durability, and moisture resistance, but it can have negative environmental impacts.
External sizing provides more flexibility, easier experimentation, and improved environmental friendliness, but it may result in inconsistent sizing and increased surface roughness.
Paper manufacturers should carefully evaluate these factors to choose the most suitable sizing method for their specific requirements and environmental goals.
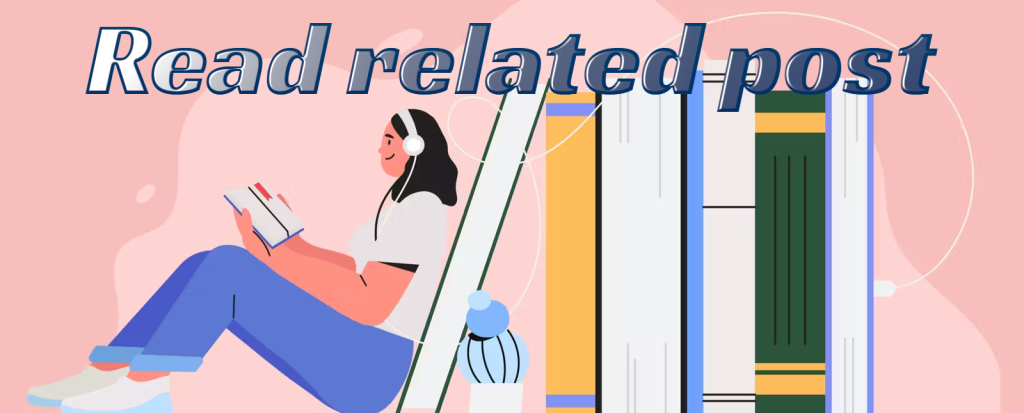