Introduction
New Labeling Requirements by OSHA: The revised Hazard Communication Standard (HCS) provides more structured requirements for the labeling of chemicals. The revised standard requires that information about chemical hazards be communicated on labels using quick visual notations to alert the worker, providing immediate recognition of the hazards. Labels must also inform workers on the proper handling of the chemical and protective measures.
OSHA Definition
OSHA defines labels as “an appropriate group of written, printed or graphic informational elements concerning a hazardous chemical that are affixed to, printed on, or attached to the immediate container of a hazardous chemical, or to the outside packaging”. The purpose of a label is to identify the contents of the material and inform the worker of the potential hazards and related safety information of the specific chemical. Accidents and fatalities have occurred when containers have not been labeled or incorrectly labeled. For example, OSHA investigated a fatality in October 2002 involving a car wash/detailing worker on his break who inadvertently drank from an unlabeled bottle assuming the contents to be water. The employee, feeling very sick after drinking the substance in the quart bottle, asked his coworkers to bring him to the hospital. He was taken to San Antonio Community Hospital where he was pronounced dead at from internal injuries. Laboratory analysis showed that he drank an acid solution from the plastic bottle containing hydrofluoric acid and phosphoric acid with a pH of less than one.
Related Post: CHEMICAL LABELING COMPLIANCE: REQUIREMENTS & SOLUTIONS
Label Elements
The HCS requires chemical manufacturers, importers, or distributors to ensure that each container of hazardous chemicals leaving the workplace is labeled, tagged or marked. The previous standard required the label to include the identity of the hazardous chemical(s), appropriate hazard warnings and the name and address of the chemical manufacturer, importer, or other responsible party. HCS now requires the following elements on labels of hazardous chemicals:
- Name, Address and Telephone Number of the chemical manufacturer, importer or other responsible party.
- Product Identifier is how the hazardous chemical is identified. This can be (but is not limited to) the chemical name, code number or batch number. The manufacturer, importer or distributor can decide the appropriate product identifier. The product identifier must be the same on the label and in section 1 of the SDS.
- Signal Words are used to denote the relative level of severity of the hazard and alert the reader to a potential hazard on the label. There are only two words used as signal words, “Danger” and “Warning.” Within a specific hazard class, “Danger” is used for the more severe hazards and “Warning” is used for the less severe hazards. There will only be one signal word on the label no matter how many hazards a chemical may have. If one of the hazards warrants a “Danger” signal word and another warrants the signal word “Warning,” then only “Danger” should appear on the label.
- Hazard Statements describe the nature of the hazard(s) of a chemical, including, where appropriate, the degree of hazard. For example: “Causes damage to kidneys through prolonged or repeated exposure when absorbed through the skin.” All of the applicable hazard statements must appear on the label. Hazard statements may be combined where appropriate to reduce redundancies and improve readability.
The hazard statements are specific to the hazard classification categories, and chemical users should always see the same statement for the same hazards no matter what the chemical is or who produces it.
Precautionary Statements
describe recommended measures that should be taken to minimize or prevent adverse effects resulting from exposure to the hazardous chemical or improper storage or handling. There are four types of precautionary statements: prevention (to minimize exposure); response (in case of accidental spillage or exposure emergency response, and first-aid); storage; and disposal. For example, a chemical presenting a specific target organ toxicity (repeated exposure) hazard would include the following on the label: “Do not breathe dust/fume/gas/mist/ vapors/spray. Get medical advice/attention if you feel unwell. Dispose of contents/ container in accordance with local/regional/ national and international regulations.”
A forward slash (/) indicates that the classifier can select one of the precautionary statements. In the example above, the label could state, “Do not breathe vapors or spray. Get medical attention if you feel unwell. Dispose of contents in accordance with local/regional/ national/international regulations.” In most cases, the precautionary statements are independent. Nevertheless, OSHA does allow some flexibility for applying precautionary statements to the label, including combining statements, using an order of precedence or removing an inappropriate statement.
Precautionary statements may be combined on the label to save on space and improve readability. For example, “Keep away from heat, spark and open flames,” “Store in a well-ventilated place,” and “Keep cool” may be combined to read: “Keep away from heat, sparks and open flames and store in a cool, well-ventilated place.” Where a chemical is classified for a number of hazards and the precautionary statements are similar, the most stringent statements must be listed on the label. In this case, the chemical manufacturer, importer, or distributor may impose an order of precedence where phrases concerning response require rapid action to ensure the health and safety of the exposed person. In the self-reactive hazard category Types C, D, E or F, three of the four precautionary statements for prevention are:
- “Keep away from heat/sparks/open flame/hot surfaces. – No Smoking.”;
- “Keep/Store away from clothing/…/ combustible materials”;
- “Keep only in original container.”
These three precautionary statements could be combined to read:
“Keep in original container and away from heat, open flames, combustible materials and hot surfaces. – No Smoking.”
Supplementary Information.
Additional instructions or information deemed helpful may be included as supplementary information. Any hazards not otherwise classified may be listed under this portion of the label. This section must also identify the percentage of ingredient(s) of unknown acute toxicity when it is present in a concentration of equal or greater than 1% (and the classification is not based on testing the mixture as a whole). If an employer chooses to include additional information about the chemical that is above and beyond the standard’s requirements, it may list this information under “supplementary information.”
Related post: THE IMPORTANCE OF PROPER LABELLING AND DOCUMENTATION IN COMPLIANCE WITH CAUSTIC SODA STANDARDS
OSHA, DOT and Shipped Containers
Any container leaving the workplace is a “shipped container.” Under paragraph (f)(l) of the HCS, each container of hazardous chemicals leaving the workplace must be labeled, tagged, or marked with the information specified in section 1910.1200(f)(l)(i)-(vi). The requirement to label a shipped container has not changed under the Hazard Communication Standard (HCS). The information required on the label has changed. Under the HCS, an employer is required to label a hazardous chemical’s immediate container, but the standards do not require labels on the outside shipping containers. When a hazardous chemical leaves the workplace, its immediate container must be labeled in accordance with paragraph (f)(l).
It is important to note that the OSHA pictograms do not replace the diamond- shaped labels that the U.S. Department of Transportation (DOT) requires for the transport of chemicals, including chemical drums, chemical totes, tanks or other containers. Those labels must be on the external part of a shipped container and must meet the DOT requirements set forth in 49 CFR 172, Subpart E. If a label has a DOT transport pictogram, the HCS states that the corresponding HCS pictogram shall not appear. Nonetheless, DOT does not regard the HCS pictogram as a conflict and for some international trade both pictograms may need to be listed on the label. OSHA will allow both DOT and HCS pictograms for the same hazard on a label. While the DOT diamond label is required for all hazardous chemicals on the outside shipping containers, chemicals in smaller containers inside the larger shipped container do not require the DOT diamond but do require the OSHA pictograms.
OSHA does not require an outside box or an overpack to be labeled with a HCS label, since they are not immediate containers. When an overpack is being utilized because a hazardous chemical’s immediate container has broken open or is leaking, the overpack needs to be labeled in accordance with the HCS. Likewise, when a shipping container is also the immediate container for the hazardous chemical, the shipping container must be labeled in accordance with the HCS.
Labels must be legible, in English, and prominently displayed. Other languages may be displayed in addition to English. Chemical manufacturers, importers, and distributors who become newly aware of any significant information regarding the hazards of a chemical must revise the label within six months.
Related post:
Employer Responsibilities
Employers are responsible for maintaining the labels on the containers, including, but not limited to, tanks, totes, and drums. Labels must be maintained on chemicals in a manner which continues to be legible and the pertinent information (such as the hazards and directions for use) does not get defaced (i.e., fade, get washed off) or removed in any way.
The employer is not responsible for updating labels on shipped containers, even if the shipped containers are labeled under HazCom 1994. The employer must relabel items if the labels are removed or defaced. However, if the employer is aware of newly-identified hazards that are not disclosed on the label, the employer must ensure that the workers are aware of the hazards as discussed below under workplace labels.
There is also no required format for how a workplace label must look and no particular format an employer has to use; however, it cannot contradict or detract from the required information.
Labels for Small Containers
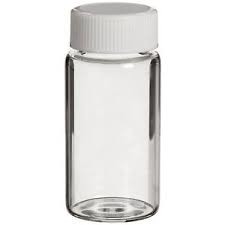
Small containers and sample jars or tubes such as 1 or 2 ounce bottles, being sent to companies or customers are difficult to label with a full size label. OSHA has provided labeling guidance for sample bottles. OSHA is allowing tags (attaching a tag to the sample bottle where the tag has all the label elements) see below:
“Tags, pull-out labels, or fold-back labels may be an appropriate way for you to label small containers so that the label elements are legible. When tags are used, they must be affixed to the immediate container of the hazardous chemical in such a way that they do not become separated from the container.”
An employer asked if the label on the small bottle due to its limited size can include product name, company ID and pictogram and refer users to the SDS. OSHA stated that it was not permitted. According to the guidance the bottle itself needs to have at least the following information:
- Product identifier,
- Appropriate pictograms,
- Manufacturer’s name and phone number,
- Signal word,
- A statement indicating the full label information for the chemical is provided on the outside package.
The small bottle is required to be stored in an outside package which could be a ziplock bag, manila envelope or pouch, or box, etc. This outside label needs to have the full label information and also state that it corresponds to a smaller bottle.
Example: Category 1 flammable liquid, named High Flam, where the only hazard is the flammability, manufactured by ABC.
The immediate container (sample bottle) must contain:
- High Flam, (product identifier),
- Flame Pictogram, (pictogram),
- DANGER, (signal word),
- ABC, (manufacturer name),
- (123) 456-7890, (phone number),
- Full labeling information for High Flam is provided on the outside package.
The outside package (ziplock bag or envelope) must contain:
- High Flam,
- Flame Pictogram,
- DANGER,
- Extremely flammable liquid and vapor, all the precautionary statements (e.g., Store in a well-ventilated place. Keep cool. Keep container tightly closed) see Appendix C, subsection C.4.19 for the full list of precautionary statements that must be present for a category 1 flammable liquid.
- ABC 100 Any Street, Any Town, MA 14569
- Phone # (123) 456-7890.
NOTE: As this is a flammable liquid, the outer packaging MUST not be of a material that is flammable or combustible, 29 CFR 1910.106(d)(2)(i).
Workplace Labels
OSHA has not changed the general requirements for workplace labeling. Employers have the option to create their own workplace labels. They can either provide all of the required information that is on the label from the chemical manufacturer or, the product identifier and words, pictures, symbols or a combination thereof, which in combination with other information immediately available to employees, provide specific information regarding the hazards of the chemicals.
If a company is utilizing a system of labeling that meets the requirements of HazCom 1994, the employer may continue to use this system in the workplace as long as this system, in combination with other information immediately available to the employees, informs them on all of the health and physical hazards of the chemical. This workplace labeling system may include signs, placards, process sheets, batch tickets, operating procedures, or other such written materials to identify hazardous chemicals. OSHA is allowing flexibility by permitting employers to utilize such labeling methods or a combination thereof may be used instead of a label from the manufacturer, importer or distributer as long as the employees have immediate access to all of the information about the hazards of the chemical. Workplace labels must be in English. Other languages may be added to the label if applicable.
Additional
instructional symbols that are not included in OSHA’s HCS pictograms can be included on workplace labels. For example, a person with goggles, indicating that goggles must be worn while handling the chemical. Including both types of pictograms on workplace labels is acceptable. Rating systems such as National Fire Protection Association (NFPA) diamonds or HMIS requirements can continue to be utilized for workplace labels as long as they are consistent with the requirements of the Hazard Communication Standard and the employees have immediate access to the specific hazard information.
If hazardous chemicals are transferred from a labeled container to a portable container that is only intended for immediate use by the employee who performs the transfer, no labels are required for the portable container. However it is highly recommended that these container be labeled as well.
Other Clarifications
A company asked OSHA whether the web address for the company can be used instead of a physical or mailing address on the required HCS 2012 label. OSHA replied that some small businesses may not have access to the internet and the physical or mailing address for manufacturer, importer or distributor is required. The company’s web address may be included on the label as supplemental information.
A company asked OSHA whether the legal name of the company (e.g., Airgas USA, LLC) be used on the HCS 2012 label or can the trade name (e.g., Airgas) be used instead. OSHA replied that the objective of including the name of the manufacturer, importer or distributor on the label and safety data sheet serves to ensure that downstream users know whom to contact if they have any questions. The trade name can be used on the label and safety data sheet (SDS) when its recognizable to downstream users. The same company name (e.g., Airgas) needs to be listed on the label and SDS. Listing the trade name on the label and the full legal company name on the SDS, may potentially create confusion and would not be compliant.
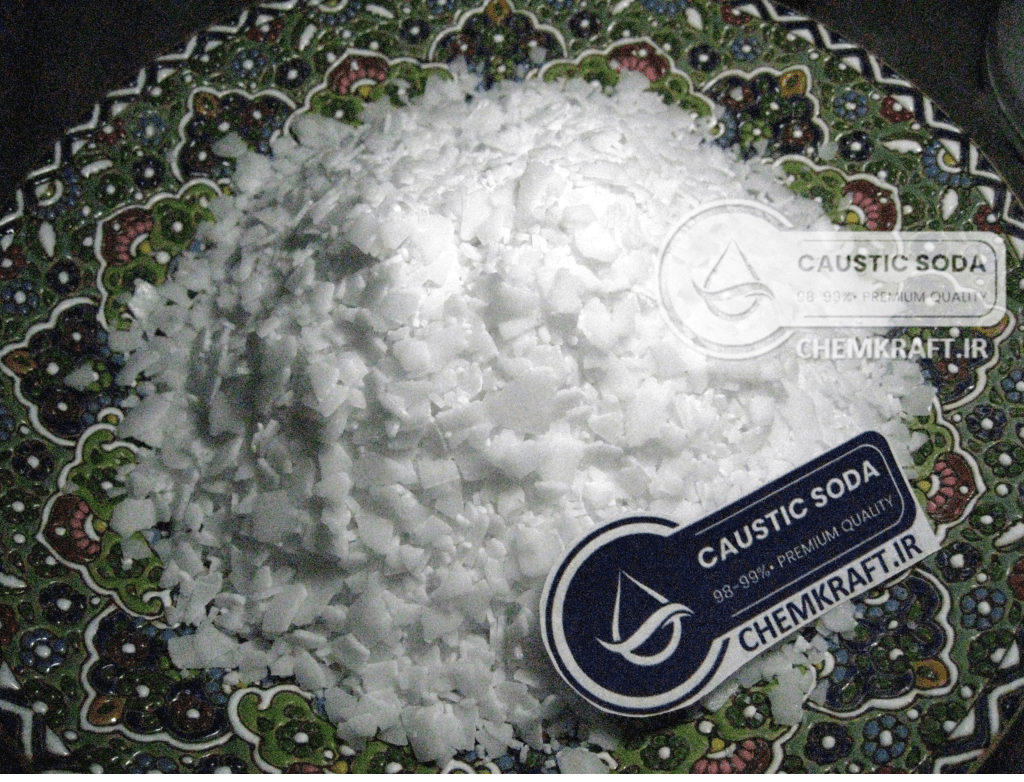


