نکاتی در مورد سایزینگ AKD
AKD یک عامل سایزینگ فعال است که میتواند با گروه هیدروکسیل سلولز واکنش داده و یک پیوند کووالانسی برگشت ناپذیر تشکیل دهـد و این اثر سایزینگ پایدار است.
مکانیسم سایزینگ AKD از سه مرحله اصلی تشکیل شـده است:
- ذرات امولسیون AKD به سطح فیبر متصل می شوند.
- AKDدر قسمت خشک کردن گرم می شود و روی سطح الیاف پخش می شود.
- AKD با گروه های هیدروکسیل سلولز واکنش می دهد تا پیوندهای کووالانسی ایجاد کند.
هنگام استفاده از امولسیون AKD برای سایز خنثی باید به این نکته توجه داشت که تولید لجن در سیستم به راحتی صورت میگیرد و برای کنترل آن در حین تولید باید قارچ کش اضافه کرد و در صورت نیاز به تمیز کاری باید خاموش شود. عوامل موثر بر اندازه خنثی AKD عمدتاً شامل جنبه های زیر است:
مقدارPH
از آنجایی که شرایط واکنش AKD در شرایط خنثی انجام می شود، کنترل pH دوغاب و سیستم هنگام افزودن AKD بسیار مهم است. محدوده pH بهینه بین 7 تا 8 است. زمانی که مقدار pH کمتر از 6 باشد، AKD کاملا بی اثر است. بنابراین هنگام تغییر سیستم از حالت اسیدی به خنثی علاوه بر شستشوی کامل سیستم میزان AKD باید افزایش یافته یا حتی دو برابر شود.
نگهداری
به طور کلی، اندازه AKD نیاز به اضافه کردن مواد کمکی نگهدارنده دارد. با توجه به افزودن عامل مقاومت مرطوب PAE، علاوه بر افزایش مقاومت مرطوب، اثر هم افزایی بر نگهداری AKD نیز دارد.
PAE (پلی آمید اپی کلروهیدرین) نه تنها در انتهای مرطوب دارای اثر ماندگاری است، بلکه در واکنش سایزینگ AKD هنگامی که ورق کاغذ خشک می شود نیز شرکت می کند.
مطالعات نشان داده است که وقتی کاغذ گرم می شود رزین PAE به یک هسـته دوست تبدیل می شود که باعث باز شدن حلقه لاکتون AKD شده و آن را روی زنجیره ماکرومولکولی رزین PAE ثابت می کند.
رزین PAE توانایی پل زدن بالایی دارد و می توانـد به صورت برگشت ناپذیر روی سطح الیاف ثابت شـود به طوری که AKD از طریق واکنش میانی با PAE به طورغیرقابل برگشتی به سطح فیبرمتصل می شود.
زمان اضافه کردن مواد
AKD تحت یک واکنش هیدرولیز در آب قرار می گیرد تا محصولی را بدون سایزینگ تشکیل دهد و این واکنش هیدرولیز با افزایش دما تسریع می یابد. در عین حال از برش شدید باید اجتناب شود. عمل برش به امولسیون AKD آسیب می رساند، بنابراین برای کاهش اتلاف AKD در کاغذسازی، زمان اضافه کردن مواد باید تا حد امکان نزدیک به قسمت فرم دهی باشد.
دما
هنگامی که دما الزامات واکنش را برآورده نکند، واکنش سایزینگ نمی تواند رخ دهد. کنترل دما و شرایط خشک کردن یک عامل مهم برای اطمینان از اثر سایزینگ است. نقطه شروع واکنش اندازه نباید کمتر از 95 درجه سانتیگراد باشد. یک مدیر تولید کاغذ باید دما و زمان مناسب را با توجه به روش های مختلف خشک کردن تنظیم کند.
در طول تولید، مشخص شد که با فرض اطمینان از درجه سایزینگ، هر چه مقدار AKD کمتر باشد، بهتر است. هنگامی که مقدار AKD از مقدار بهینه بیشتر شود، کاهش مقدار cobb (جذب) کند می شود و در عین حال ضریب اصطکاک کاغذ کاهش می یابد و کاغذ دچار لغزش می شود و تولید مشکل می شود. میزان سایزینگ کاغذ AKD دارای پسماند است.
معمولاً محصول را باید 7 تا 10 روز پس از بیرون آمدن ازدستگاه نگهداری کرد تا به تدریج اثر سایزینگ به دست آید.
بنابراین برای اندازه گیری میزان سایزینگ کاغذ نیـمه آماده باید با عمل خشک کردن در کوره 105 درجه سانتیگراد به مدت 10 دقیقه درجه رسیدن سایزینگ را تسریع کرد. نتیجه سایزینگ شـده در این زمان درجه سایزینگ نهایی است.
در تابستان سایزینگ کاغذ توسط AKD مشکل سختی سایزبندی را ندارد به راحتی خشک می شـود و نیازی به رزین امولسیون شـده ندارد. پس از محاسبه اقتصادی هزینه هر تن کاغذ کمتر از تولید کاغذ اسیدی خواهد بود و استحکام کاغذ حدود 10 درصد افزایش می یابد.
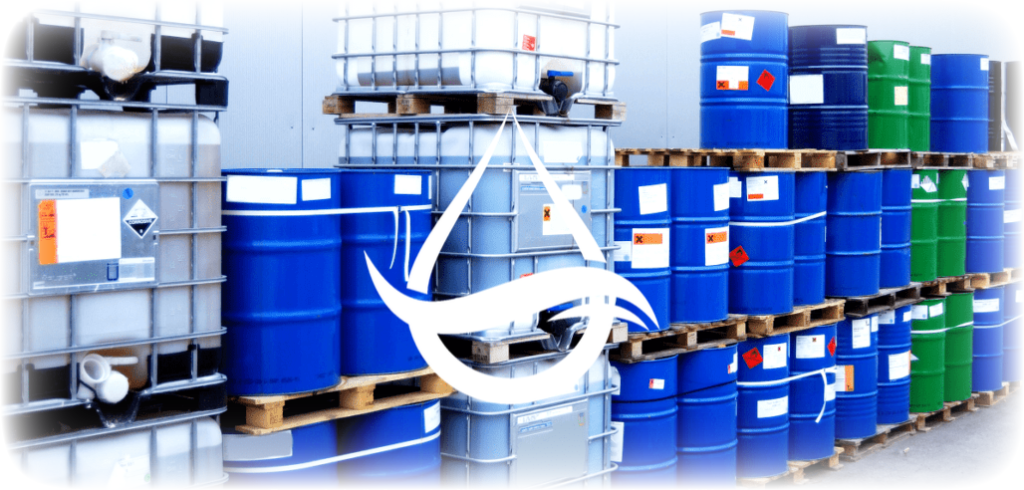